Power from Not-So-Hot Geothermal
Power from Not-So-Hot Geothermal
http://www.technologyreview.com/read_article.aspx?id=17524&ch=energy
This power system could make it feasible to generate cheap electricity from lukewarm geothermal sources.
A large share of the geothermal resources suitable for power generation--those with temperatures higher than 300°F--are deep underground, beyond the reach of current technology. Lower-temperature resources, which are common across the United States, are generally used for heating, but could be a bountiful source of power as well, if researchers were able to find an economical way to convert them into electricity.
Engineers at the United Technologies Research Center (UTRC), a unit of United Technologies based in East Hartford, CT, say they have developed a low-cost system that can utilize low-temperature geothermal resources. The technology could be particularly useful in generating electricity from waste hot water generated at oil and gas wells.
The modular, 200-kilowatt power plant from UTRC can convert temperatures as low as 165°F into electricity. The technology is similar to steam engines, except that steam or hot water vaporizes a hydrofluorocarbon refrigerant that drives the turbine. And the refrigerant has a lower boiling point than water. "It's hard to run a steam engine at 165 degrees [Fahrenheit]," says Bruce Biederman, who leads the project at UTRC. "The size of the equipment would be enormous and your turbine would be very poor in efficiency."
The UTRC power plant can be thought of as a reverse cooling system, and the new turbine is essentially a refrigerator compressor running backwards, Biederman says. Instead of using power to create a temperature difference, like a refrigerator does, it converts a temperature difference into electricity.
The company is now testing a unit at a remote hot springs resort 60 miles northeast of Fairbanks, Alaska. Biederman expects a commercial power plant to be ready by early next year, after they've tested the reliability of the demonstration system.
According to him, the system could utilize the large amount of hot water pumped out of the ground at oil and gas wells. In Texas alone, more than 12 billon barrels of water are produced from wells. Oil companies usually discard the waste water by re-injecting it into the earth; but they could use it to generate electricity. Biederman is planning to set up demonstration projects at oil and gas wells in Texas and Nevada next year.
This reverse cooling concept isn't new; but until now no one has made an efficient turbine at a reasonable cost, he says. UTRC has kept down costs by modifying refrigeration units that its sister company, Carrier Corp., makes, and using its production line in Charlotte, NC.
The system's small size also keeps costs down, and makes it more usable, says Maria Richards, who coordinates the geothermal laboratory at Southern Methodist University in Dallas. "The fact that it can fit on the back of a flatbed truck and be driven to a well site makes it much more convenient and less expensive," she says. "It's [like comparing] a mainframe computer and a laptop." And, as with other renewables, increasing fuel costs are spurring interest in geothermal power units, she adds.
Gwen Holdmann, vice president of new development at the Alaskan hot springs resort where the technology is being tested, says they spent $2.2 million on the UTRC geothermal power plant, and that it should pay for itself in five years. "It could even be a quicker payback if the cost of fuel keeps rising," she suggests. Before the power plant was installed, the resort was burning $1,000 worth of diesel fuel per day to generate electricity, she says. The plant eliminates those costs and the harmful emissions from diesel generators.
Right now, geothermal power plants are located mainly in the western United States, where high-temperature steam or hot water appears naturally at the surface. Drilling wells to reach high-temperature resources deep underground can cost millions of dollars, yet still be cost-effective because they're efficient for power generation, Richards says. So far, however, it hasn't been economical to use lower-temperature geothermal resources for power.
But existing oil and gas wells, where electricity generated from waste hot water could run the oil pumps, would be the ideal location for the UTRC power modules, Richards says. "They're already drilling wells, the wells are already being used, and they're producing something that is a secondary source of energy

Chena Geothermal Power Plant
http://www.yourownpower.com/Power/
Project Overview ...
Alaska has more geothermal resources than any other state in the country, and yet none of these resources has been developed for power generation prior to 2006. In 2004, Chena Hot Springs Resort entered into a partnership with United Technologies Corporation (UTC) to demonstrate their moderate temperature geothermal ORC power plant technology at Chena Hot Springs.
The Chena geothermal power plant came online in late July 2006, putting Alaska squarely on the map for new geothermal technologies. Chena Hot Springs is the lowest temperature geothermal resource to be used for commercial power production in the world. We hope this will be the first step toward much greater geothermal development in the state. The cost of power production, even in semi-remote locations such as Chena, will be reduced from 30¢ to less than 7¢ per kWh once the UTC plant is installed and operational.
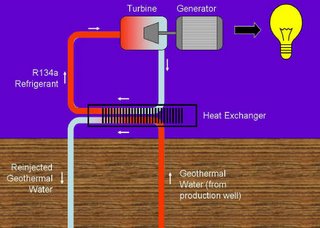
The challenge for moderate temperature small scale geothermal development has been to bring the cost down to a level where it is economical to develop small geothermal fields. UTC has been working toward that goal. In the past, small geothermal power plants have been built to order using tailor made components, which has greatly increased both the expense and the lead time for such units.
UTC’s Research Center has teamed up with their sister divisions, Carrier and UTC Power, to reverse engineer mass produced Carrier chiller components to dramatically reduce the cost of production, and allow for modular construction. UTC has already proven this technology with the release of their PureCycle 200 power plant in 2003, which is designed to operate off waste heat applications.
How it Works ...
Because the geothermal water at Chena Hot Springs never reaches the boiling point of water we cannot use a traditional steam driven turbine. Instead a secondary (hence, "binary") fluid, R-134a, which has a lower boiling point than water passes through a heat exchanger with 165°F water from our geothermal wells. Heat from the geothermal water causes the R-134a to flash to vapor which then drives the turbine. Because this is a closed loop system virtually nothing is emitted to the atmosphere. Moderate temperature is by far the most common geothermal resource and most geothermal power plants in the future will be binary cycle plants. Here are the steps in the cycle:
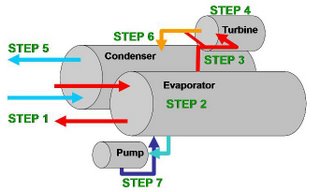
STEP 1: Hot water enters the evaporator at 165ºF (480gpm). After the hot water runs through the evaporator, it is returned to the geothermal reservoir via our injection pump and injection well system. Some of the water is also used to heat buildings on site before it is reinjected.
STEP 2: The evaporator shell is filled with R-134a, a common refrigerant found in many air conditioning systems. The 165ºF water entering the evaporator is not hot enough to boil water, but it is hot enough to boil the R-134a refrigerant. The evaporator is a giant heat exchanger, with the hot water never actually coming in contact with the refrigerant, but transferring heat energy to it. The R134a begins to boil and vaporize.
STEP 3: On initial system startup, the vapor bypasses the turbine and returns directly to the condenser via a bypass valve. Once there is adequate boiling/evaporation of the refrigerant, the bypass valve closes and the vapor is routed to the turbine.
STEP 4: The vapor is expanded supersonically through the turbine nozzle, causing the turbine blades to turn at 13,500rpm. The turbine is connected to a generator, which it spins at 3600rpm, producing electricity.
STEP 5: Cooling Water enters from our cooling water well which is located 3000ft distant and 33ft higher elevation than the power plant. Cold water (40ºF-45ºF) is siphoned out of this well and supplied to the power plant condenser at a rate of 1500gpm.
STEP 6: The cooling water entering the condenser and recondenses the vapor refrigerant back into a liquid. As in the evaporator, the condenser only allows heat transfer to occur between the refrigerant (in the shell) and the cold water (in the tubes within the condenser). The two liquids never actually come in contact.
STEP 7: The pump pushes the liquid refrigerant back over to the evaporator, so the cycle can start again. By doing so, it also generates the pressure which drives the entire cycle.
Carrier Chillers versus UTC Power Plant
The concept of running a refrigeration cycle in reverse to generate power has been known for a long time. However, until now the refrigeration industry has never seriously pursued this idea. When Carrier Refrigeration was conducting performance tests on the 19XR centrifugal chiller, a high reverse rotational speed was noted that during simulated power outages. This is typical in a refrigeration unit, as pressures between the condenser and evaporator equalize during shutdown. However, the 19RX chiller was designed using a discrete passage diffuser, rather than the vaneless diffuser used on previous products. The vaneless diffuser was observed to allow reverse rotational speeds up to 75% of normal operating speeds, and this triggered the idea of actually using the compressor as a turbine. Carrier further developed this concept with their sister divisions, United Technologies Research Center and United Technologies Power, ultimately resulting in the 2004 release of the PureCycle™ 200. The PureCycle™ uses waste heat exhaust gases and air cooled condenser equipment. The Chena Power plant takes the PureCycle™ concept one step further, generating power economically off a 120°F temperature differential between the evaporator and condenser temperature. Interestingly enough, this approaches the temperature differential of the air-conditioning unit the power plant was derived from. For this reason, the same refrigerant typically used in Carrier Refrigeration systems can be used for the Chena power plant.
One big advantage of using refrigeration or air-conditioning equipment for power generation is that the hardware used for these applications has a cost structure substantially lower than that of traditional power generating equipment. By keeping as many components the same as possible, the UTC Power Plant can substantially reduce construction costs by taking advantage of Carrier's mass production line. In fact, if a Carrier Refrigeration mechanic were to come to Chena Hot Springs, they would not be able to tell the different between our turbine/generator assembly and a Carrier compressor/motor.
There are three main changes made to transform a Carrier chiller into a power plant. The turbine/generator assembly has 13 of 171 parts uniquely manufactured for power production versus its corresponding chiller/compressor assembly. A pump has been added to circulate the liquid refrigerant and maintain operating pressure. Also, the heat exchangers, while standard Carrier manufactured units, are specifically sized for power plant operation at design temperature.
Download a FACTSHEET on the geothermal power plant
0 Comments:
Post a Comment
<< Home